We all know about the environmental dangers of computers and phones but how bad are synthesizers and drum machines for the planet?
Modern electronic devices are wonderful and make our lives generally easier but this convenience can come at a cost to the environment. Devices like computers and smartphones often come under scrutiny for their impact on the environment and accordingly, changes are being made. Companies that make environmental safety a major selling point are starting to emerge as well, such as outfits like Fairfone. Headphone and speaker brand AIAIAI Audio touts its use of recycled materials and vegan leather. It’s even made its way into the vinyl manufacturing industry.
Where do musical instrument and production hardware companies stand on this issue? There seems to be less of a conversation happening around sustainability and environmental protection when it comes to synthesizers, drum machines and studio gear in general. How much of an impact does the manufacture and disposal of the gear that we use and love have on our planet?
Take Warning
The Guide To Greener Electronics, periodically published by Greenpeace, is an analysis of the environmental impact of major electronics manufacturers and IT companies like Apple, Google and Samsung. The last report, published in 2017, found that the supply chain – including manufacturing – accounted for 70 to 80% of the carbon footprint generated during the lifetime of a product. While there’s no similar report for electronic musical instruments and studio gear, we can assume that the data would be similar.

To find out what kind of an impact gear is having on the environment and how companies are addressing these issues, we reached out to two manufacturers, Focusrite and Roland.
Towards Net Zero Carbon Emissions
The biggest impact on the environment comes from the manufacturing process, as outlined in Greenpeace’s report. Emissions are categorized in three ways. Scope 1 emissions are those generated by your own company, such as on-site power plants or vehicles directly owned. The next category, Scope 2, includes emissions created by the generation of electricity, heat or steam by power companies that are purchased by the manufacturer. Scope 3 emissions, however, are harder to calculate because they are entirely indirect. They include all emissions incurred by the manufacturing process of suppliers, among other things.
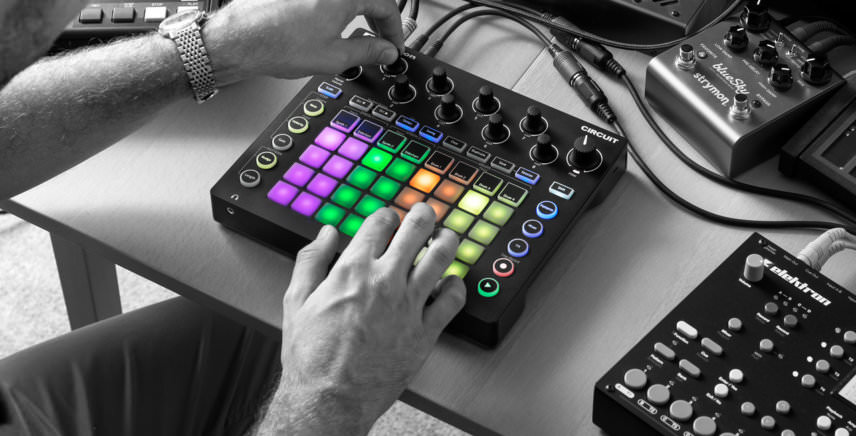
“We published our full emissions last year, and I think … 99.87% was our Scope 3 emissions.” We’re speaking with Andy Land, who is Head of Sustainability at Focusrite Group, which includes Martin Audio, Optimal Audio, ADAM Audio, Sequential, Linea Research, Oberheim, Novation, Ampify Music, Sonnox and Focusrite itself. “Basically all of it is our products that we make.”
The goal is net zero carbon emissions. This is different from carbon neutral, which only involves purchasing carbon offsets. Net Zero requires reductions in emissions of at least 90% first, before balancing out the remaining residual footprint with removals. “Ultimately, that’s where we want to get to and hopefully go beyond that,” says Andy. This will involve a combination of purchasing carbon offsets and focusing on reducing their Scope 3 emissions. “The thing we’ve got to do is take apart (our) products, work out where the hotspots are, and try and swap those ones out for more environmentally friendly options. It’s just grinding away at that across 300 or so products across the entire group.” This product range includes synthesizers, MIDI controllers, audio interfaces, studio monitors, and more.
Roland is also committed to reducing its carbon footprint. “We are engaging in measures to contribute to the reduction of CO2 emissions and to increase the efficiency of business activities,” the company states on its website. It also reports its total CO2 emissions, including those from Scope 3.
Reducing Scope 3 Emissions
Unlike Scope 1 emissions, which companies can reduce by being mindful of their activities and processes, Scope 3 emissions are a little more tricky, mainly because much of it is out of their hands, such as the use of the product once sold. “The power consumption of all of our products, if you take a really high-level view, is probably about 60% of our footprint,” notes Andy. They can design product power use to be as efficient as possible but ultimately power grids themselves will need to be revamped. “If electricity grids clean up, that 60% (will be) achieved without us doing anything. So that leaves a really difficult 30%, which is raw materials, and 10% is kind of everything else: logistics, recycling, end of life and a few other bits that contribute to that.”
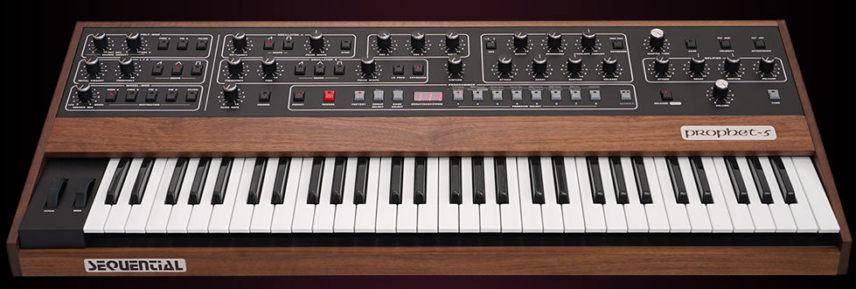
Roland is also aiming for more efficient products. One way is by including “energy saving designs in early stages of development,” according to the company, such as high-efficiency power circuits, auto-off functions, and other Scope 3-reducing features.
Recyclable Materials
One way that companies can reduce CO2 emissions is during the manufacturing process and using recycled materials instead of new ones. It’s much cheaper to melt down existing aluminum from products than to “go dig a big hole and get new aluminum out of the ground,” says Andy.

Rather than use newly sourced aluminum, polycarbonates (a kind of plastic used in engineering), and other commonly used products, Focusrite are trying to use recycled materials wherever possible. However, high-percentage, post-consumer recycled plastic tends not to hold together very well. “The problem is when you get to that kind of level of recycled content, plastic degrades every time you recycle it so it starts to crumble apart,” laments Andy. The solution is to use mostly recycled plastic but 100% remains out of reach – so far. Focusrite and others are actively testing and working to reach this milestone.
Aluminum, thankfully, is infinitely recyclable. “But the problem with aluminum,” notes Andy, is availability. “You’ve got the likes of Coca-Cola wanting to buy recycled aluminum for all their cans. We’re small in electronics, relatively, (but) we’re even smaller compared to Coca-Cola.”
Focusrite’s recently released fourth-generation Scarlett Audio Interface is the first time for the company where they’ve been able to take all of what they’ve learned and apply it to a single product. “You’ve got the post-industrial recycled aluminum chassis that’s on every product, (and) you’ve got the post-consumer recycled ABS plastic, that’s 85%, which is a pretty good percentage to have.”
Packaging: “It’s About Designing To Be Efficient”
Packaging is also important when considering the environmental impact of a product. “That was the thing that took the most effort with the fourth generation Scarlett, looking at the packaging in detail,” says Andy.
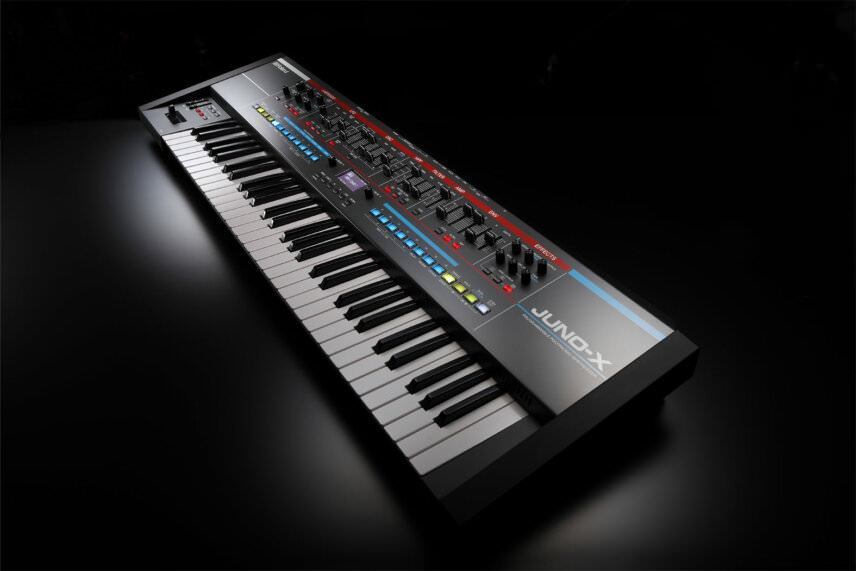
Some ways that Focusrite has changed packaging include swapping out the protective polyethylene plastic product bag for a starch-based bag, using paper tape instead of plastic tape, and rearranging the placement of items inside the box to reduce volume and thus get more boxes on a palette or in a shipping container. “It’s just about designing it to be efficient,” sums up Andy.
Roland has also focused on shipping efficiency, reducing the volume of its boxes to move more products at a time. And while customers may bemoan the disappearance of paper manuals from hardware boxes, using downloadable PDF versions makes more sense from an environmental standpoint.
Product Recycling
Another aspect of Scope 3 emissions is the product’s end-of-life cycle. Hopefully, users aren’t just throwing away synthesizers but the modern consumerfication of musical instruments may be contributing to a disposable mindset. “While electronic take-back programs are growing, the speed of collection cannot keep pace with the rate of consumption,” notes Greenpeace.
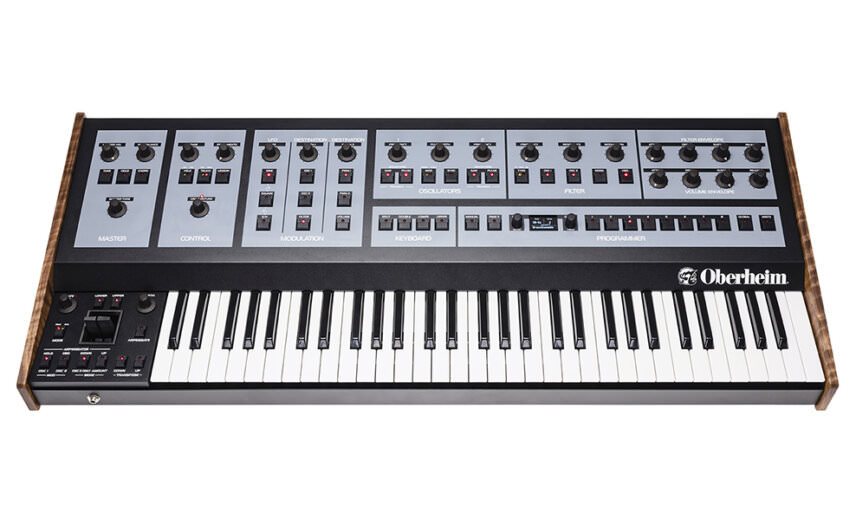
One way to encourage longer use of a product is with periodic updates that extend the item’s usefulness. “Software and content updates enable long-term product availability and reduce product waste,” says Roland.
Of course, it’s unrealistic to assume a consumer will hold onto a product forever. “Our products probably fall more in that category of things that do end up in drawers rather than get recycled at the moment,” notes Andy. “We’re trying to put ourselves within this circular economy where we’re taking raw materials from old products, and our products can be easily disassembled and turned into other products,” says Andy. “That’s the end goal: we get this closed loop where everything fits together.”
Towards The Future
We as if Focusrite is trying to make the perfect product, environmentally speaking, but Andy wonders if that would even be possible. “I think the ultimate goal is not necessarily to create a perfect product. I’m not entirely sure that … you can ever have electronics with no impact. But we are on this pathway to reach net zero, ultimately. That’s where we want to get to and hopefully go beyond that. And that means we’ve got to achieve a 90% reduction in our footprint compared to a baseline year, which we’re still yet to set.”
One way that companies across the industry can ensure they are hitting their goals is by working together. Companies tend not to share data of any kind. This is understandable from a business point of view, but an exception should be made in terms of the environment.
With this in mind, Andy helped form a cross-company group called Greening Music Tech, which shares just this kind of data. “We want to become leaders (in this area) and try and encourage the whole industry to improve, he says, “hence we’ve got this working group.” Currently, there are 54 members across 17 companies involved, including Ableton, Native Instruments and D&B Audiotechnik.
Summing up everything, Andy says, “It’s going to take time. It’s not something you can solve overnight.”
It will ultimately be worth it though.